既存設備を活かしながら
レーザ発振器を更新
当社オリジナル光学設計からの提案により必要な機器だけの更新を可能に。
PROPOSER
レーザ部門は当社の技術者がお客様それぞれのレーザアプリケーションや加工条件(材料・加工品質・タクト・コスト等)のニーズを満たす製品を提案し、レーザ関連機器をお客様にお届けしています。独自の光学設計からお客様の要望に合わせて最適なレーザ製品を提案しています。
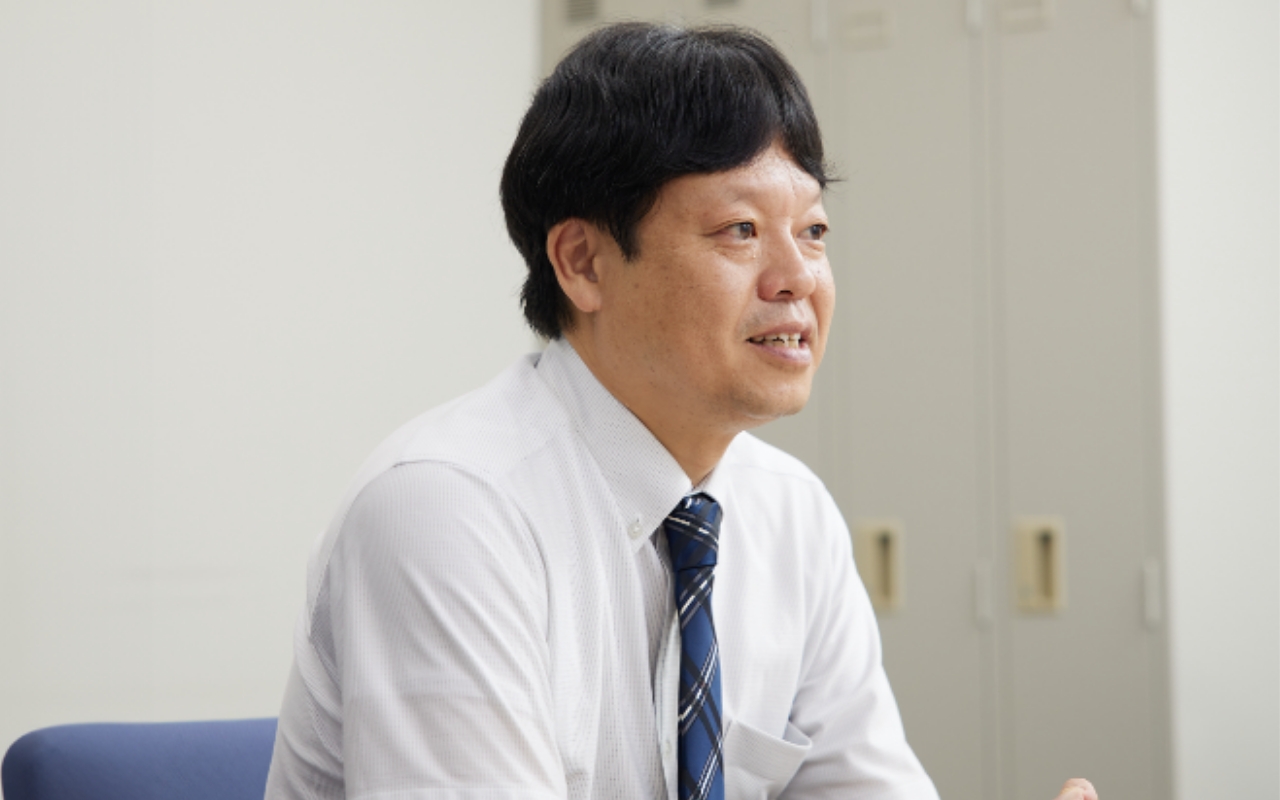
BEGINNING
お客様である自動車メーカー様の製造ラインにおいて、レーザ溶接工程の効率アップとランニングコストの低減を目的として、レーザ発振器を旧式のYAGレーザからファイバーレーザに更新されたいというニーズがありました。
レーザ発振器の仕様が異なるため、どのレーザメーカーもレーザ発振器を更新することでロボットに搭載する加工ヘッドやファイバー等システムを一式で更新する提案をしていました。
そのため設備更新費用が高額となり、なかなか導入に踏み切れない状況でした。
弊社がレーザ関連機器を光学設計から提案できることをアピールするためお伺いしましたところ、本件提案のご機会をいただきプロジェクトがスタートいたしました。
もっとレーザ発振器を更新することでのシステム全体の投資費用を下げられないか
お客様の製造ラインでは非常に多くのレーザ溶接装置が稼働しており、どの装置も導入から一定の年月を経過していました。 今後は予防保全的にもレーザ溶接装置の設備更新は避けては通れない課題となっていました。
レーザ機器は日々進化しており、近年は変換効率が高くランニングコストが低いファイバーレーザが主流となってきています。 お客様の製造ラインはほぼすべてが旧式のYAGレーザであったため、設備更新においてファイバーレーザに変更することを検討されていました。 お客様が複数のレーザメーカーに相談されたところ、既存の設備である加工ヘッドも含めて下流側システムを一新するプランばかりで、レーザ発振器を更新することでの1台あたりの見積が非常に高額でした。
そこで弊社に、導入コストを下げる提案をしてほしいとお声がけいただきました。
TECHNOLOGY
独自の光学系設計技術が必要に
お客様の製造ラインでは抵抗溶接の7倍の加工速度を実現するリモートレーザー溶接が工程短縮のため使われていますが、なかでもレーザ溶接用光学機器は専用の仕様となっているためコストがかなりかかります。通常はレーザ発振器が更新により仕様が変わると加工ヘッドも発振器の仕様に合わせて変更しないと使用できなくなり新たに加工ヘッド・ファイバー等を設計・製作して作り変える必要が生じます。
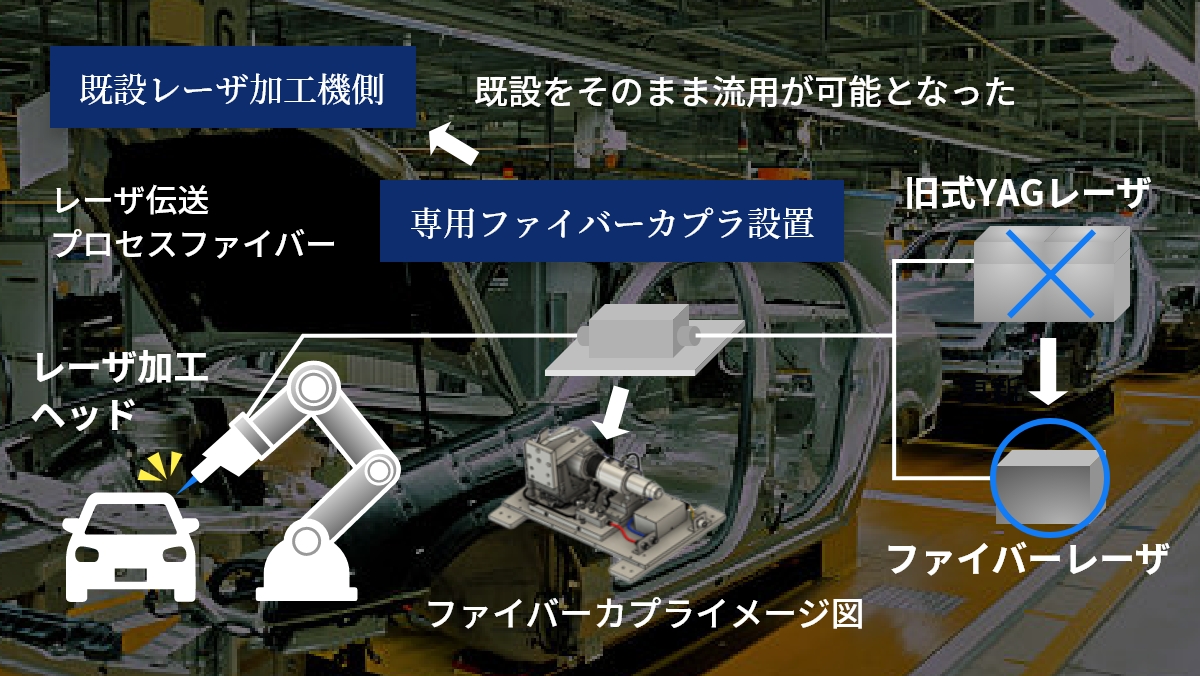
弊社には経験豊富なレーザ専門の技術者が在籍していますので、さっそく今回の案件に関して検討を開始しました。
どうすればレーザ発振器を更新する事でのシステム全体の投資費用を低く抑えることができるかについて時間をかけて検討し、加工ヘッド等下流側は既存の設備を使用してレーザ発振器だけを入れ替える、独自の光学設計が可能な弊社ならではの提案が可能となりました。
そのためには、レーザ発振器と加工ヘッド等下流側設備との間にコア径の異なる異種ファイバーの光学的なカップリングを可能とする機器(ファイバーカプラ)を提案致しました。ただ開発には独自の光学系の設計技術が必要であり、だれでもが簡単に開発できるものではありません。弊社には高度な光学設計ができる技術者がいたからこそ、チャレンジできたのだと思います。
SOLUTION
1台あたりの設備更新コスト1/3を達成
最初は半信半疑であったお客様も、何度か試作を繰り返すうちに弊社の技術に大きな期待を持っていただけるようになりました。その後に無事に最初のファイバーカプラが導入され、今では同様のレーザ溶接設備すべてにファイバーカプラが導入されました。導入後ファイバー挿抜後の現地調整を省略したいとの新たな要望にも応え専用アライメント治具を設計することにより工場で出荷前にその治具によるアライメントをすることで光軸調整済みの製品として現地での作業も大幅に省略できるようにもなっております。
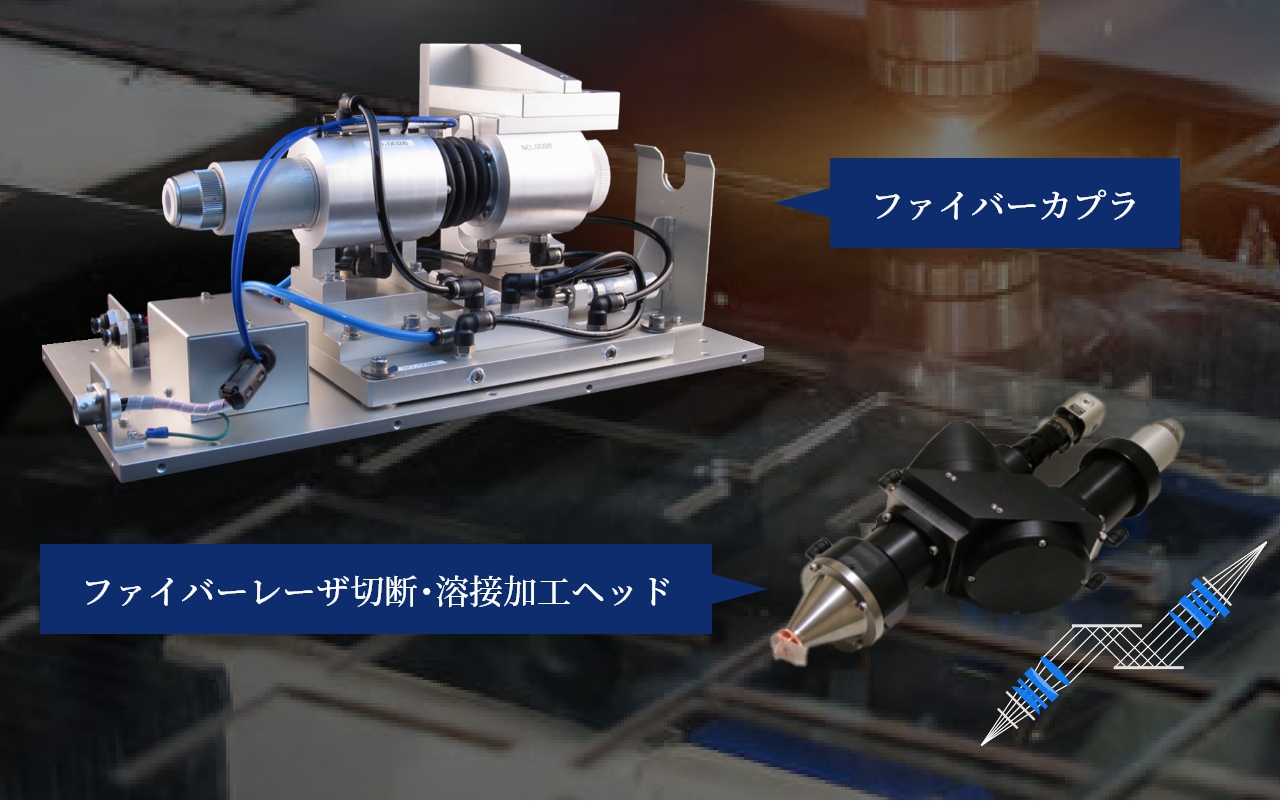
このファイバーカプラを使用するシステムであれば、レーザ発振器の設備更新における導入コストを従来の1/3に抑えることが可能となり、多くのお客様から高いご評価をいただいています。
当社には他社にはない独自の光学設計の技術力がありオリジナルのファイバーカプラ、加工ヘッド等の光学機器を設計・製作することが可能です。今後もその技術で様々な課題解決を提案していきたいと思います。
SOLUTION STORY
課題解決事例を見る